Колесные центры унифицированной колесной пары изготовлены из стальной отливки и состоят из ступицы, обода и диска.
Рис.14. Колесный центр:
1-ступица; 2-диск; 3-обод.
Отлитые центры для получения однородной и мелкозернистой структуры металла и снятия внутренних напряжений подвергают отжигу. Колесные центры напрессовывают на ось с усилием 1100—1500 кН (ПО— 150 тс) при насаженных и 950—1400 кН (95—140 тс) при ненасаженных бандажах. Натяг между посадочными поверхностями составляет 0,18— 0,3 мм. Действительный натяг и качество прессового соединения определяют по диаграмме усилий, снимаемой при запрессовке. Диаграмму прикладывают к паспорту каждой колесной пары.
Катаные колесные центры применяют как опытные. Их также подвергают термической обработке. Применение катаных колесных центров позволяет снизить массу (неподрессоренную) до 45 кг на каждом центре и уменьшить динамическое воздействие на рельсовый путь.
Бандажи являются той частью колес, которая непосредственно взаимодействует с рельсами. На контактную площадку бандажа передаются вертикальные силы до 150 кН (15 тс), продольные силы сцепления до 45 кН (4,5 тс) и поперечные — до 30 кН (3 тс) на поверхности катания и до 80 кН (8 тс) на гребень. Материал бандажа подвергается растяжению, сжатию, сдвигу и смятию, а при скольжении колес усиленному износу. В связи с этим материал бандажа должен обладать высокой прочностью, чтобы сопротивляться износу и смятию, и быть достаточно вязким, чтобы сопротивляться ударным нагрузкам. Бандажи подвергают термической обработке путем закалки и последующего отпуска. На наружные диаметры колесных центров насаживают бандажи с натягом 1,1 — 1,45мм тепловым способом. Температура нагрева бандажа 523-593 К (250—320°С). Разность температур различных участков бандажа при нагреве не должна превышать 323 К (50°С).
Рис.15. Бандаж:
1-колесный центр; 2-бандаж; 3-бандажное кольцо;
Бандажи на колесных центрах закрепляют бандажными кольцами. Бандажные кольца заводят в специальную выточку, когда температура бандажа не ниже 473 К (200° С), и закатывают роликом на специальном станке внутреннюю кромку бандажа до плотного крепления кольца. На собранной колесной паре разность твердостей бандажей не должна превышать НВ20.
После остывания проверяют (по звуку) плотность посадки бандажа на колесный центр. Для контроля отсутствия проворачивания бандажей колесной пары относительно колесных центров при эксплуатации тепловоза на бандажах и колесных центрах наносят контрольные риски и кернение. Окончательная обточка бандажей по профилю производится после их насадки.
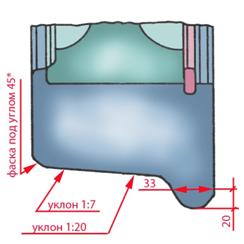
Для обеспечения безопасности движения и стабильных качеств ходовой части тепловоза предельный прокат поверхности катания не должен превышать 7 мм, износ гребня — 8 мм (толщина 25 мм) и минимальная толщина бандажей колесных пар по кругу катания — 36 мм. Интенсивность образования проката характеризуется износом в мм на 104 км пробега тепловоза и зависит от степени использования мощности, профиля пути, нагрузки от колесной пары на рельсы и других факторов.
Опыт эксплуатации показал, что интенсивность проката колес тепловозов для среднесетевых условий составляет 0,38 мм на 104 км пробега. Интенсивность износа гребня при протяженности кривых на участке эксплуатации около 50 % составляет 0,8 мм на 104 км пробега. Это вызывает необходимость преждевременной обточки колес для восстановления профиля бандажей по износу гребней. Толщина слоя снимаемого металла, определяемая по износу гребня, значительно больше, чем это требуется для восстановления профиля поверхности катания. Срок службы бандажей сокращается.
С целью уменьшения износа гребней бандажей и увеличения срока их службы ВНИИЖТом предложен новый объединенный профиль локомотивов и вагонов. Объединенный профиль снижает давление в контакте и обеспечивает относительно свободное поперечное перемещение колесной пары в колее. Угол наклона образующей гребня к горизонту составляет 65°. Радиус выкружки гребня 15 мм, согласованный с радиусом скругления рельсовой головки, обеспечивает наименьшее контактное давление на выкружке гребня.
Испытания показали, что бандажи с объединенным профилем будут иметь меньший на 20—30 % износ гребней по сравнению со стандартным. Износ по кругу катания остается на уровне стандартного профиля.
Буксы передают вертикальные и горизонтальные (тяги и торможения, поперечные от набегания на рельс) силы между рамой тележки и колесными парами. Кроме того, буксы ограничивают продольные и поперечные перемещения колесной пары относительно рамы тележки. Вертикальные статические нагрузки на буксы достигают 100—ПО кН (10—11 тс), а при движении тепловоза они возрастают в 1,3—1,5 раза. Одновременно на буксовые узлы действуют продольные тяговые и тормозные усилия около 20—25 кН (2—2,5 тс), удары колес на стыках, вызывающие ускорения букс (7—25g), и рамные усилия до 50—75 кН (5—7,5 тс) при частоте осевого нагружения 1,5—2,0 Гц. Совокупностью этих действующих сил определяется конструкция буксового узла, которая должна обеспечивать прежде всего безопасность движения, эксплуатационную долговечность подшипников не менее 1,8 млн. км пробега.
Конструкция буксового узла показана на рисунке.
Корпус 9 буксы с двумя кососимметрично расположенными поводками 2 соединен с рамой тележки. Соединение валиков поводков с корпусом буксы и рамой тележки производится посредством клиновых соединений и болтами 1. Литой корпус буксы имеет также и два боковых опорных кронштейна (крыла) для установки пружин рессорного подвешивания тележки и восприятия вертикальной нагрузки. В цилиндрическую расточку корпуса буксы до упора в заднюю крышку 6 установлены по скользящей посадке два роликовых подшипника и между ними дистанционное кольцо 10. С целью повышения срока службы подшипники устанавливают в одном буксовом узле с разностью радиальных зазоров не более 0,03 мм. Кроме того, потолок корпуса буксы выполнен в виде свода переменного сечения увеличенной толщины верхней части, что дает не только более равномерное распределение нагрузки между роликами, но и увеличение числа роликов, находящихся в рабочей зоне. На предподступичную часть оси до упора в галтель надето с натягом лабиринтное кольцо 3. Температура нагрева кольца 393—423 К (120—150° С). Лабиринтное кольцо образует с задней крышкой 6 четырехкамерное лабиринтное уплотнение буксы. Внутренние кольца подшипников имеют натяг 0,035—0,065 мм и насажены на шейку оси вместе с дистанционным кольцом 11 нагретыми в индустриальном масле до температуры 373—393 К (100—120 °С). Для предотвращения сползания с шейки оси внутренних колец роликоподшипников служит стопорное кольцо 12.

Рис.16. Буксовый узел:
1, 21 - болты; 2 - поводок; 3 - лабиринтное кольцо; 4 - стопорный болт; 6- задняя крышка: 7, 22 - шелковый шнур; 8 -роликоподшипник; 9 - корпус буксы; 10, 11 —дистанционные кольца; 12,14- стопорные кольца; 13 кронштейн; 15 упорный шарикоподшипник;
16- амортизатор, 17 -передняя крышка; 18 -пружина; 19 - упор; 20 -контровочная проволока; 23 - коническая пробка;
В передней крышке 17 монтируется осевой упор качения одностороннего действия через упорный шарикоподшипник, одно кольцо которого установлено на торцовой проточке оси, а другое — на упоре 19 с натягами 0,003—0,016 мм. В целях предотвращения раскрытия упорного подшипника он постоянно через упор 19 пружиной 18 прижимается с усилием около 2 кН (200 кгс) к торцу оси колесной пары. Осевой упор удерживается стопорным кольцом 14 в крышке 17 при ее снятии. Между упором и крышкой установлен амортизатор 16, представляющий собой две металлические пластины толщиной 2 мм с привулканизированным между ними резиновым элементом. В буксах средних колесных пар амортизатор не ставится, обеспечивая тем самым свободный осевой разбег ±14 мм (равный толщине амортизатора) этих колесных пар в буксах. На передней крышке приварен кронштейн 13 для присоединения гасителя колебаний.
Для того чтобы отличать буксы колесных пар от букс средних колесных пар, на крышках букс наносятся знаки «КР» для крайних и «СР» для средних. На задней крышке установлен стопорный болт 4, предотвращающий сползание буксы с шейки оси при снятой с тепловоза колесной паре.
Смазка для буксового узла единая пластичная. При сборке буксы закладывают смазку ЖРО в лабиринтное уплотнение задней крышки, подшипники и осевой упор передней крышки в количестве 2,5 кг. Дозаправка смазки в буксовый узел в процессе эксплуатации производится запрессовкой через отверстие с конической пробкой 23, расположенное в нижней части корпуса буксы.
Поводок буксы состоит из корпуса 7 с двумя головками, имеющими цилиндрические расточки, в которые запрессованы с натягом 0,06......0,16 мм амортизаторы, сформированные один на коротком, другой на длинном валике. Короткий валик 8 (буксовый) имеет одну резинометаллическую втулку 12. Длинный валик 5 (рамный) имеет две резинометаллические втулки 3, между которыми помещены разделяющие их полукольца 1.
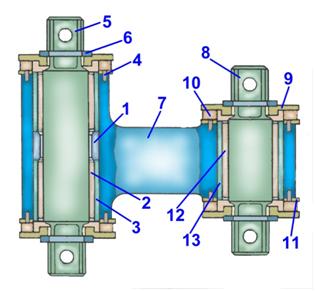
Рис.17. Поводок буксы:
1,6-полукольца; 2,3,12,13 –резино-
металлические втулки; 4 - штифт; 5 - рамный валик; 7- корпус; 8- буксовый валик; 9 - кольцо; 10- резиновый элемент; 11 - шайба
Амортизаторы формируют на валики напрессовкой. Перед напрессовкой резиновые втулки и все соприкасающиеся с ними поверхности смазывают смесью, состоящей из 30 % касторового масла и 70 % этилового спирта. Сформированные поводки выдерживают в течение 20 дней при температуре 288—293 К (15—30° С) без доступа света и приложения нагрузки для завершения релаксационного процесса сцепления резины с металлом.
Валики имеют трапециевидные (клиновидные) хвостовики для установки их в соответствующие пазы на раме тележки и корпусе буксы. Крепятся хвостовики болтами М20х80, момент затяжки не менее 150 Н • м (15 кгс • м). На хвостовики валиков установлены с натягом торцовые амортизаторы, состоящие из кольца 9, шайбы 11 и привулканизированного к ним резинового элемента 10, и крепятся с помощью разрезных полуколец 6, вставляемых в выточки валиков. С поводками они соединяются штифтами 4, вследствие чего при повороте поводка в вертикальной плоскости резиновые элементы торцовых амортизаторов работают на сдвиг. Клиновидные хвостовики длинного и короткого валиков у верхних поводков имеют встречное направление, у нижних — попутное.
Коэффициент жесткости поводков одной буксы в поперечном направлении составляет 35 • 105—45 • 105 Н/м (350—450 кгс/мм), а в продольном — 235 • 105—275 • 105 Н/м (2350—2750 кгс/мм). Такая упругая поперечная связь между колесными парами и рамой тележки да еще в сочетании с буксовым осевым упором одностороннего действия значительно улучшает горизонтальную динамику тепловоза.
Шестерня изготавливается из стали 12Х2Н4А. Поверхности зубьев и впадин шестерен цементируют на глубину 1,6—1,9 мм (после шлифовки) и подвергают закалке до твердости HRC³59; твердость сердцевины зуба и обода — HRC³35. С целью повышения усталостной прочности при изгибе шестерен исходный профиль впадин зубьев выполняют с выкружками (протуберанцами) и не шлифуют. Продольных скосов зубья шестерен не имеют, как на прежних жестких передачах, а влияние перекоса компенсируется самоустанавливающимся зубчатым венцом упругого колеса. После закалки и шлифовки профиль зуба и впадин шестерни подвергают магнитной дефектоскопии.
Посадка шестерни производится в нагретом до 443 К (170° С) состоянии на конический (конусность 1:10) хвостовик вала якоря тягового электродвигателя с осевым натягом 1,3 -1,45мм. Перед насадкой шестерни на вал сопрягаемые их посадочные поверхности проверяют на прилегание по краске (прилегание должно быть не менее 75 %). На валу электродвигателя шестерни от сползания с конуса в нагретом состоянии дополнительно крепят гайкой с моментом затяжки 500 Н • м (50 кгс • м) и контрятся отгибочной шайбой. Для съема шестерни гидрораспрессовкой на торце вала электродвигателя предусмотрено резьбовое отверстие с выходом на сопрягаемую посадочную поверхность под установку специального ручного гидронасоса.
Зубчатое колесо состоит из зубчатого венца 6, который через упругие элементы 1 и 2 посредством тарелок 19, призонных втулок 4, болтов 11 и гаек 3 соединен со ступицей 20, насаженной на ось колесной пары с натягом 0,16-0,22 мм, и жестко центрирован через ролики 10 по ее сферической поверхности. Момент затяжки болтов крепления тарелок 80 - 90 Н • м (8—9 кгс • м).
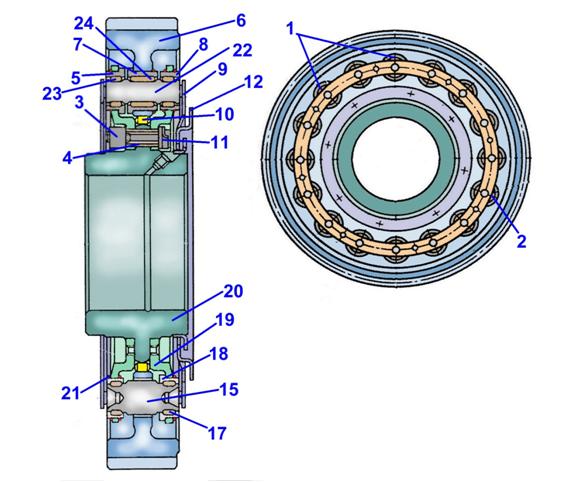
Рис.20. Зубчатое колесо:
1,2 - упругие элементы; 3 - гайка; 4 - призонные втулки; 5,7,8,16,18 - втулки; 6 - зубчатый венец; 9 - кольцо; 10 - ролик; 11- болт; 12-отражательное кольцо; 13- шайба; 14 - полукольцо; 15,22 -пальцы; 17,23,24- амортизаторы; 19- тарелка; 20-ступица; 21- пружинное кольцо;
Зубчатый венец изготавливают из стали 45ХН. Рабочая поверхность зубьев подвергается секторной закалке токами высокой частоты на глубину 3—5 мм и по .высоте 4—б мм от впадины зуба до твердости HRC³50, твердость сердцевины зуба и обода венца НВ255—НВ302. Впадины зубьев упрочняют накаткой роликами диаметром 120 мм с усилием 85—95 кН (8500—9500 кгс). После закалки и шлифовки профиль зуба и впадины венца подвергают магнитной дефектоскопии.
Упругие элементы для получения нелинейной характеристики тангенциальной жесткости зубчатого колеса выполнены разной жесткости двух типов. Восемь элементов 1 (малой жесткости) имеют жесткость (125—135)104 Н/м (125—135кгс/мм) и установлены в отверстия диаметром 70 мм тарелок и зубчатого венца по скользящей посадке. Они состоят из пальца 22, на наружную профильную поверхность которого насажены резиновые амортизаторы 24 и 23, предварительно вставленные в металлические втулки 5, 7 и 8. Втулки 5 и 7 выполнены с ограничительными буртами, препятствующими одностороннему свободному осевому перемещению по ним венца. Поэтому сформированные упругие элементы 1 устанавливают на колесе по четыре ограничительными буртами на каждой стороне зубчатого венца. Упругие элементы в тарелках и венце закрепляют стопорными пружинными кольцами 21.
Восемь других упругих элементов 2 имеют большую жесткость, равную (47—50) 106 Н/м (470—500 кгс/мм). Они установлены в отверстия тарелок по скользящей посадке, а в отверстие венца — с радиальным зазором 4 мм. Упругий элемент 2 также состоит из профильного пальца 15, на концы которого напрессованы резиновые амортизаторы 17, предварительно вставленные в металлические втулки 16 и 18. Для предотвращения сползания втулка 16 имеет ограничительный бурт и проточку, а втулка 18 — две проточки под установку стопорных пружинных колец 21. Необрезиненная поверхность пальца выполнена бочкообразной (радиусом 270 мм).
Все резиновые амортизаторы упругих элементов изготовляют из маслобензостойкой резины. Формирование упругих элементов производится способом запрессовки резиновых амортизаторов в металлическую арматуру, при этом посадочные поверхности предварительно смазывают смесью из 30 % касторового масла и 70 % этилового спирта. Сформированные упругие элементы для стабилизации сцепления резины с металлом выдерживают в течение 20 дней при температуре 288—303 К (15—30° С) без нагружения и доступа света.
При сборке упругого зубчатого колеса между венцом и ступицей устанавливают без сепаратора 90 роликов 10 размером 15х25 мм, которые обеспечивают относительное поворачивание венца и ступицы через тело качения, жесткую их центровку и разгрузку упругих элементов от радиальных усилий в зубчатом зацеплении тяговой передачи. Для возможности самоустановки зубчатого венца поверхность ступицы под роликами выполнена сферической радиусом 300 мм и упругие элементы сформированы с зазорами до 5 мм между ограничительными буртами втулок. Поверхности венца и ступицы под роликами термообработаны до твердости HRC³ 48. В целях предотвращения выпадания пальцев 15 и 22 с наружных сторон тарелок прикреплены ограничительные кольца 9. Тарелки, втулки и пальцы изготовлены из стали 45 или 38ХС и термообработаны с целью повышения износостойкости гнезд под упругие элементы.
Передача вращающего момента зубчатым колесом, имеющим упругие элементы разной жесткости двух типов, осуществляется как бы в два этапа: сначала при малом вращающем моменте в работу вступают упругие элементы 1 с меньшей жесткостью, а затем с увеличением вращающего момента (при трогании) венец поворачивается, и при угле поворота примерно Г вступают в работу более жесткие элементы 2. Таким образом обеспечивается требуемая нелинейная характеристика тангенциальной жесткости упругого зубчатого колеса.
Для осмотра состояния деталей упругого зубчатого колеса при ремонтах, а также замены упругих элементов предусмотрена возможность полной его разборки без расформирования колесной пары. Разборка производится в сторону противоположного колесного центра.
Применение в тяговом редукторе упругого зубчатого колеса позволило значительно (в 3 раза) снизить динамические нагрузки, возникающие в зацеплении при движении тепловоза, и, как показал опыт эксплуатации тепловозов, главное — достичь эксплуатационной долговечности зубчатой передачи не менее 1,2 млн. км пробега.
Для создания масляной ванны и предохранения зубчатых колес и шестерен от песка, пыли и других абразивных материалов тяговая зубчатая передача помещена в кожухе.
Кожух тягового редуктора состоит из двух разъемных сварной конструкции половин верхней 1 и нижней 12 с линией разъема по центрам шестерни и зубчатого колеса. Между верхней и нижней половинами кожуха для уплотнения разъема по всему периметру в паз, образованный приваренными изнутри и снаружи верхней половины кожуха накладками, укладывают уплотнительную резиновую трубку 6. Скрепляют две половины четырьмя болтами 7 через прокладки 8 толщиной, обеспечивающей установку уплотнительной трубки по разъему с преднатягом.
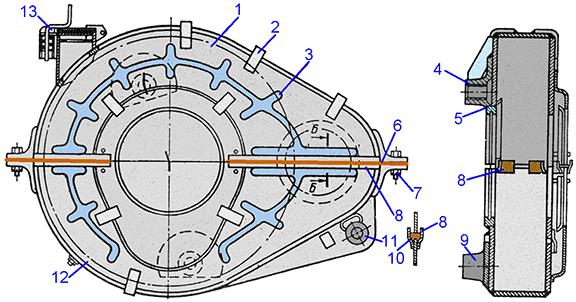
Рис.21. Кожух тягового редуктора:
1 – верхняя часть кожуха; 2 – скобы; 3 – ребра жесткости; 4, 9, 11 – бонки; 5 – полукольцо отбойное; 6 – прокладки; 7 – болты; 8 – накладки уплотнительные; 10 – уплотнение; 12 – нижняя часть кожуха; 13 – горловина для заливки масла.
Кожух центрируют горловиной по бурту вкладыша осевого подшипника и жестко крепят к остову тягового электродвигателя в трех точках болтами М42 через две бонки 4 и 9, приваренные к несущей боковой стенке вблизи центра зубчатого колеса для восприятия основной массы кожуха, и бонку 11, приваренную на нижней половине к листу и обечайке для обеспечения правильной установки кожуха относительно зубчатого колеса. С помощью прокладок, устанавливаемых под бонки крепления, регулируют зазор между торцами зубчатого колеса и стенками кожуха (который должен быть не менее 8 мм), а также радиальный зазор между ступицей колесного центра и горловиной кожуха (который должен быть не менее 1,5 мм). Регулирование зазоров необходимо из-за износа осевого подшипника в процессе эксплуатации. Момент затяжки болтов должен быть 1400—1600 Н • м (140—160 кгс • м).
Кожух от внешней среды в месте соприкосновения горловины с буртом вкладыша осевого подшипника уплотняют войлочными полукольцами, уложенными в пазы горловины, а по отверстию монтажа ведущей шестерни установкой с преднатягом войлочного кольца между стенкой кожуха и подшипниковым щитом тягового электродвигателя. По оси уплотнение кожуха выполнено бесконтактным с дополнительным расширительным коробом, который имеет отражательное полукольцо 5 и в нижней части отверстие для возврата проникшей смазки снова в полость кожуха. Герметичность сварных соединений кожуха проверяют керосином. Особое внимание уделяют уплотнению между кожухом и осевым подшипником, так как смазки разные и их смешивание резко снижает работоспособность рассматриваемых узлов и особенно польстерного устройства смазки осевого подшипника вследствие замасливания фитилей вязкой смазкой зубчатой передачи. Это уплотнение выполнено бесконтактным лабиринтно-кольцевым, образованным отбойным кольцом на ступице зубчатого колеса и желобом, который удерживается полукольцами (по одному на каждой половине), приваренными внутри на несущей боковине кожуха. На пути уплотнения в нижней части полукольца имеется отверстие, которое служит для отвода проникшей через уплотнение смазки за пределы кожуха.
Зубчатая передача тягового редуктора смазывается способом окунания, при котором зубчатое колесо захватывает смазку из нижней части кожуха и подает на рабочую часть зацепления с зубьями шестерни. В нижнюю половину кожуха заливается смазка СТП в количестве 5 кг. При этом зубья колеса погружаются в масло, не превышая окружности впадин, которое благодаря своим высоким показателям вязкости создает на поверхности зубьев непрерывный стабильный смазочный слой и в то же время стекает в нижнюю часть кожуха. Смазка СТП зубчатой передачи тягового редуктора, как показал опыт эксплуатации, обладает хорошей влагостойкостью и устойчивостью к окислению, имеет высокий показатель вязкости и удовлетворительные смазывающие качества при низких температурах 223 К (—50° С). Для предупреждения повышения давления газов в кожухе на его верхней половине установили сапун, соединяющий полость кожуха с атмосферой.
В эксплуатации контроль уровня смазки и ее дозаправку производят через горловину, закрытую резьбовой пробкой. Уровень смазки ограничивается нижним краем заправочной горловины.
Подвешивание тягового электродвигателя на раму тележки выполнено упругим пружинным и так, чтобы можно было без труда опустить полностью колесно-моторный блок и выкатить его из-под тепловоза без выкатки тележки. Это подвешивание называют обычно траверсным. Траверсное подвешивание состоит из нижней 11 и верхней 4 балочек с приваренными к ним накладками 5 и 10 из стали 20Х, цементированных и закаленных до твердости HRC³50. Между накладками расположены четыре пружины 3, предварительно затянутые усилием около 40 — 50 кН (4—5 тс) с помощью стяжных болтов 2. Собранная траверса помещается между четырьмя опорными приливами кронштейна 6 поперечной балки рамы тележки. Через крайние пружины и опоры кронштейна тележки устанавливают направляющие стержни 9, предупреждающие выпадание всего траверсного подвешивания. Крайние пружины удерживают направляющие стержни, а средние — специальные трубчатые выступы 3, приваренные к балочкам. Направляющие стержни удерживаются от выпадания снизу валиками 7, закрепленными болтами к кронштейну рамы тележки.
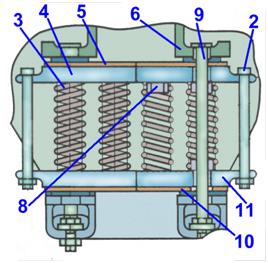
Рис.22. Подвешивание тягового электродвигателя:
2-стяжной болт; 3-пружина; 4, 11-верхняя и нижняя балочки; 5, 10-накладки; 6-кронштейн рамы тележки; 8-трубчатый выступ; 9-направляющий стержень
Установка колесно-моторного блока на тележку производится при повернутом двигателе приблизительно на 30° к горизонтали путем спуска рамы тележки или подъема колесно-моторного блока для заведения опоры (носика) двигателя на траверсу, установленную на раме тележки. После установки тягового электродвигателя 1 отпускают стяжные болты, создавая зазор 5 мм между гайками и их опорными поверхностями. При этом траверсу устанавливают с преднатягом в кронштейне тележки и с незначительным зазором в опоре двигателя для обеспечения поперечных и продольных перемещений колесно-моторного блока, которые возникают при движении
тепловоза. Упругая пружинная траверсная подвеска тягового электродвигателя смягчает удары, передаваемые на раму тележки при колебаниях колесно-моторного блока во время движения. Пружины подвески рассчитывают так, чтобы при развитии наибольшей силы тяги между витками оставался зазор. Однако при движении тепловоза колесно-моторный блок совершает колебания, которые могут быть особенно интенсивными при боксовании вплоть до полной осадки пружин. Это вызывает отрыв от поверхности контакта и большие ударные нагрузки, которые передаются на узлы подвешивания тягового электродвигателя. Кроме того, опорная часть двигателя при движении перемещается по балочкам траверсы (особенно средней колесной пары тележки) как в продольном, так и в поперечном направлении. Все это вызывает интенсивный износ трущихся деталей: накладок траверсы и двигателя, кронштейнов тележки, которые после пробега 400 тыс. км подлежат периодической замене или восстановительному ремонту.